Mechanical (HVAC) Maintenance
-
HVAC System Management: Ensure the cooling, heating, and ventilation systems are running optimally, especially critical in a data center where temperature control is crucial.
-
Routine Inspections: Regular checks on compressors, evaporators, and condensers to detect any performance issues.
-
Filter Replacements: Regular replacement of air filters to maintain airflow and air quality.
-
Preventive Maintenance: Cleaning ducts, checking refrigerant levels, and assessing cooling towers to avoid system failures.
-
Energy Efficiency: Optimizing HVAC performance to reduce energy consumption, critical for cost savings and sustainability

Electrical System Maintenance
-
Power Distribution System (PDU, UPS): Regular inspections of electrical systems including power distribution units, UPS, and backup generators.
-
Circuit Breaker & Panel Maintenance: Testing and inspection of electrical panels and circuit breakers to ensure no issues with power supply.
-
Load Testing: Regular load testing of electrical equipment and backup power systems to ensure capacity to handle demand.
-
Voltage Stabilization: Ensure voltage regulation to prevent surges, sags, or electrical faults, which can damage sensitive equipment.
-
Lighting Systems: Maintenance and energy-efficient upgrades of lighting within the facility.

Plumbing Maintenance
-
Water Leak Detection: Identifying and fixing leaks in plumbing systems that could disrupt operations or damage equipment.
-
Water Supply Systems: Ensuring a reliable water supply for systems like cooling towers or other equipment requiring water input.
-
Drainage Systems: Maintenance of drainage systems to prevent clogging or water damage.
-
Water Treatment: Ensuring water quality standards for cooling systems, preventing scale build-up, and avoiding operational issues in HVAC systems.
Fire Protection and Safety Systems
-
Fire Suppression Systems: Regular inspection and maintenance of fire suppression systems such as sprinklers, FM200, or gas-based systems.
-
Alarm Systems: Testing and calibration of fire alarms and smoke detectors.
-
Emergency Lighting: Ensuring emergency exit lighting and alarm systems are fully operational in case of power failure or emergency situations.
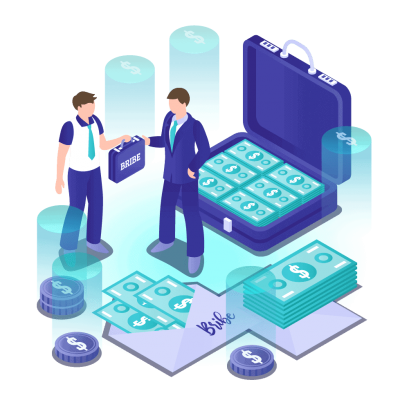
Building Management Systems (BMS)
-
Automation Systems: Monitoring and maintaining Building Management Systems for integration of MEP systems (HVAC, lighting, power, etc.).
-
Monitoring & Control: Remote monitoring of key systems and automatic control of energy consumption, air quality, and temperature.
-
System Integration: Ensuring that the mechanical, electrical, and plumbing systems are fully integrated into a centralized control system for efficient operation.
Preventive Maintenance & Troubleshooting
-
Routine Inspections: Regularly scheduled inspections of mechanical, electrical, and plumbing systems to identify potential issues before they lead to failure.
-
System Diagnostics: Troubleshooting and rectifying any MEP-related faults or inefficiencies to minimize downtime.
-
Preventive Strategies: Implementing strategies for reducing wear and tear on critical systems to extend the lifespan of equipment.
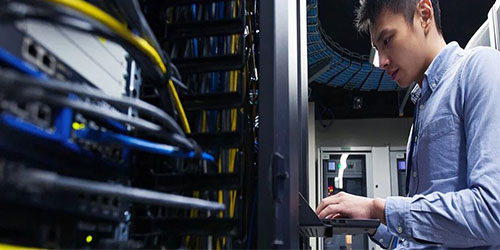
Energy Management & Sustainability
-
Energy Audits: Conducting energy audits to identify inefficiencies and propose measures for reducing energy consumption.
-
Sustainable Practices: Implementing energy-efficient technologies (e.g., LED lighting, variable-speed drives) and reducing the carbon footprint of MEP operations.
-
LEED & Green Building Standards: Ensuring systems are compliant with environmental and sustainability standards like LEED certification.
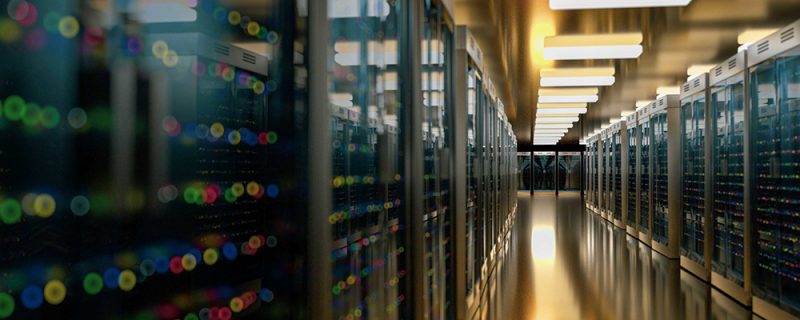
Compliance & Safety
-
Regulatory Compliance: Ensuring that all MEP systems comply with local codes and international standards (e.g., NFPA, NEC, ASHRAE).
-
Safety Protocols: Regular safety inspections and compliance with OSHA standards to ensure safe operations within the facility.
-
Documentation & Reporting: Keeping detailed maintenance logs, reports, and certificates for inspections and audits.
Vendor Management and Coordination
-
Third-Party Support: Coordinating with external vendors for specialized MEP repairs, parts replacement, or system upgrades.
-
Contract Management: Managing service contracts for the repair and replacement of MEP systems.
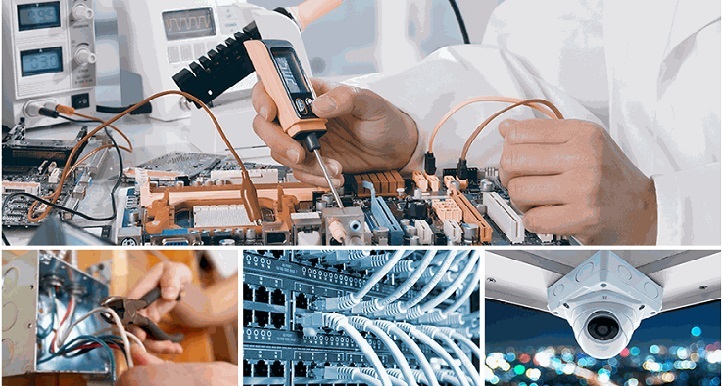